Charged with a complex bridge topographic survey, Horrocks Engineering and Spicer Group deliver results in one-third of the time with significantly more data thanks to their innovative approach.
In March 2019, the Idaho Department of Transportation entrusted a pair of engineering companies with creating a full topographic survey of the Clearwater Memorial Bridge and surrounding area as part of a multiyear project to replace it and surrounding roadways, ensuring safe and efficient transportation for generations to come.
The job fell first to Horrocks Engineers, which has 15 offices throughout the western United States, including three in Idaho. Collecting survey data for the bridge and surrounding roadways was a standard job for their mobile mapping unit, said Lonnie Olson, principal and survey manager at Horrocks, but the project also called for bathymetric data for the river bottom and bridge substructure.
“They wanted a look at the scour around the bridge pilings,” Olson said. “One of the avenues they’re looking at is to keep the substructure and much of the bridge itself.” He knew that adding multibeam sonar data to the mobile mapping cloud data would give the resulting topo consistent, fine-grained, accurate data from the river bottom on up, but there was a problem: Horrocks doesn’t have a multibeam sonar unit.
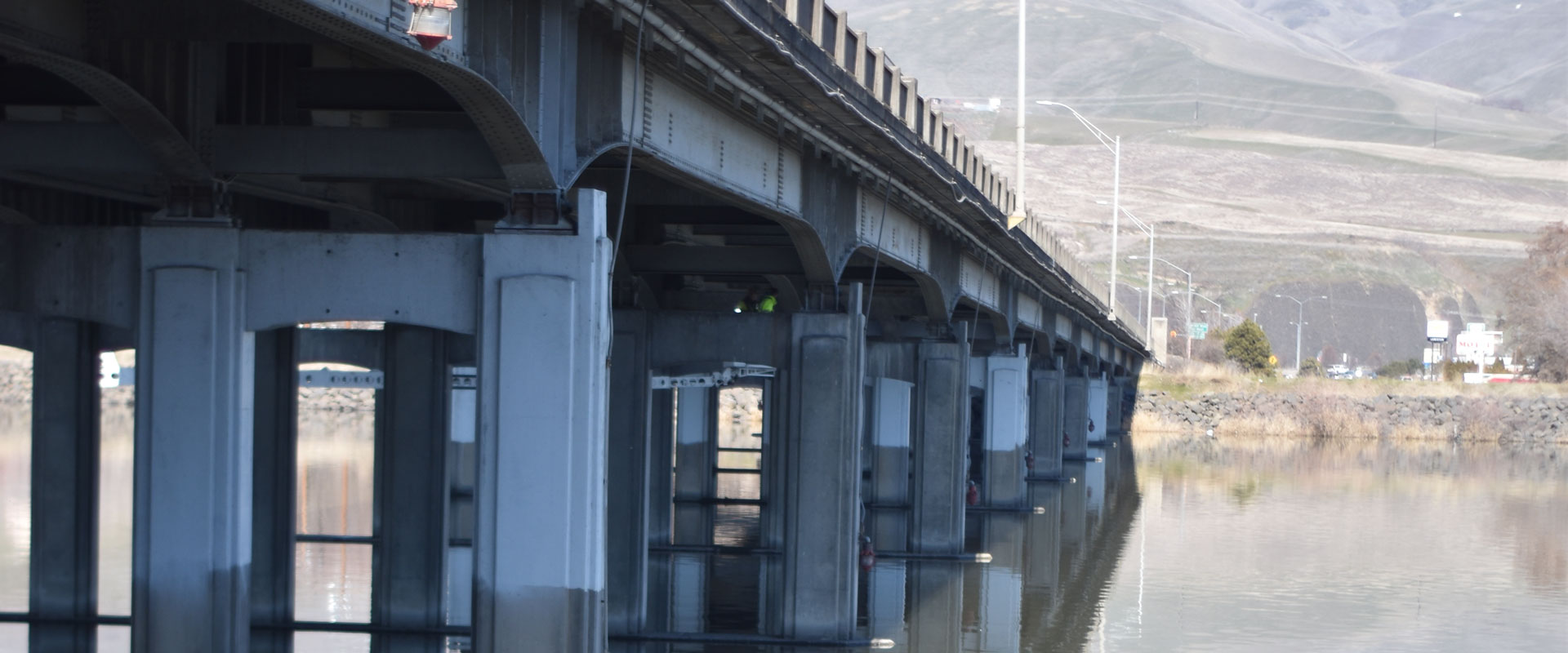
“In Utah,” where Olson is based, “we don’t have any big rivers, and most of the lakes don’t require much bathymetric data,” Olson said. “We normally just do single-beam sonar, which isn’t what we were looking for here.”
Olson researched his options and learned that Spicer Group, based in Saginaw, Mich., has a multibeam unit for just this kind of bridge-scour analysis and hydraulic modeling. Even better, Spicer’s sonar vessel is also fitted with a Leica Pegasus:Two Mobile Sensor Platform for its above- and below-waterline mobile mapping—the same mobile scanning platform Horrocks invested in 18 months prior for its roadway mapping. Olson decided to reach out to Spicer Project Surveyor Nathan Shepherd and combine forces on the job — the first time he’d ever subcontracted out to another surveying team.
Mobile LiDAR Provides Significant Time Savings
Horrocks would drive the bridge and surrounding roadways. Spicer would drive the river to get everything below waterline, the river banks, and the underside of the bridge. Then they’d stitch the data together, extracting the planometrics to create a surface model and topographic survey. Because the Pegasus is a sensor platform capable of ingesting data from multiple sources, the multibeam and LiDAR information could be seamlessly integrated into a single point cloud.
Spicer drove its survey vessel 35 hours from Saginaw, Mich., to Lewiston, Idaho, for the job. “You can’t just go out and rent a boat and make it work,” said Spicer’s Nathan Shepherd.
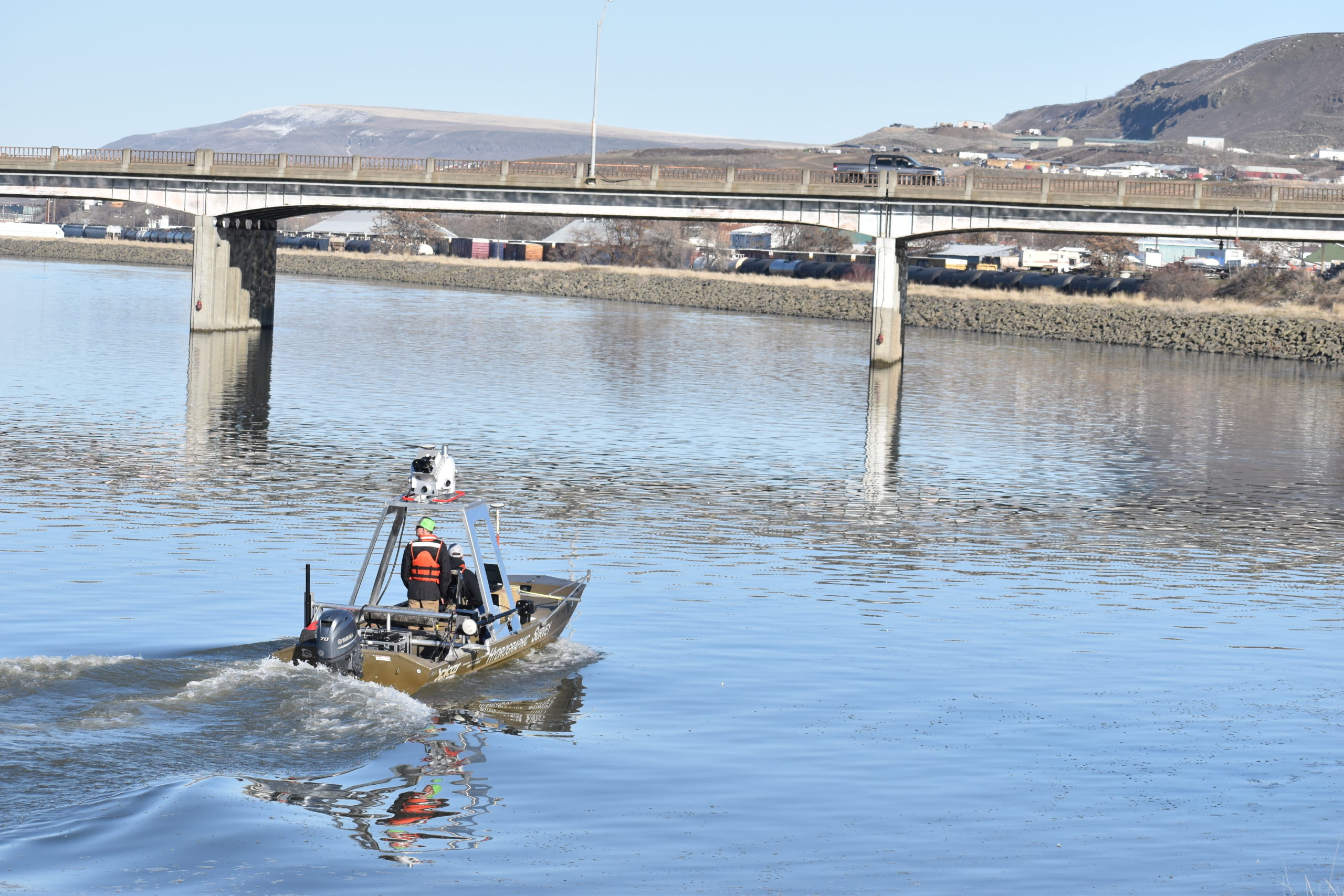
First, Spicer had to drive the 18-foot flat-bottom boat, fitted with a 60-hp outboard, 35 hours to Lewiston from Saginaw, Mich. “The mount for the Pegasus is bolted to the boat,” Shepherd said, “and that’s the third iteration we’ve tried, so that it was in the right location and not in the way of the guys when they were driving. The multibeam on the bottom, that’s the fourth or fifth generation of mounting to get it just right. You can’t just go out and rent a boat and make it work.”
And while Spicer did, indeed, end up scanning both the river bottom and underside of the bridge at the same time, it doesn’t actually make sense to run both units simultaneously on most projects.
“That always sounds great for marketing,” laughed Shepherd, “but the multibeam doesn’t collect nearly the same amount of data that LiDAR does.” While the Pegasus’ LiDAR unit could grab everything with just a single pass back and forth under the bridge and along the river banks, the multibeam is a bit more like mowing the lawn, Shepherd explained. The team needed 40 or 50 passes with the multibeam to get the bottom of the river and the data necessary for all the clearance elevations and hydraulic study.
Still, the data collection was all done in a day.
All told, it took about three days to set up the full control network for the job, then four days onsite preparing and doing the actual scanning, for a total of seven days in the field—a significant time savings compared to traditional methods.
“You would never find that kind of accuracy any other way. You could achieve it, but the cost would be exponential.”
– Olson
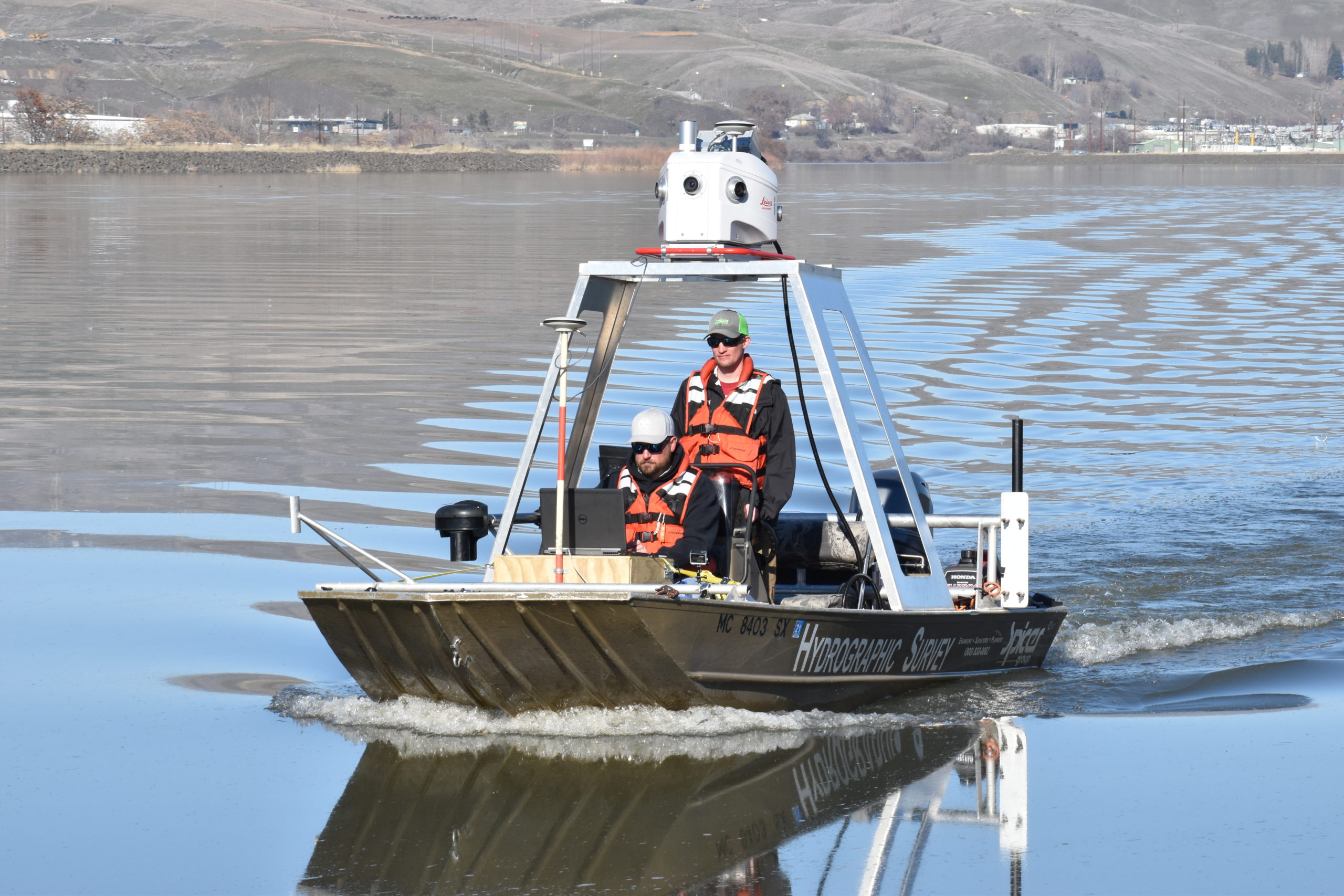
“Ten years ago,” said Olson, “you would have had to cross section every 50 feet with a robotic total station, and shoot in some key points of the structure, and you’d have to spend probably three to four weeks onsite doing control and collection.”
As for the underwater work, you’d probably have a cross section every 250 feet, maybe a dozen total measurements with single-beam sonar, and then a model from that, said Shepherd. “And they wouldn’t have been able to get the scour. There would be no way to know about that,” he said. “They would have had to send divers down to visually look at it.
“So, it’s about one third of the time,” Shepherd summarized, “and I don’t know how many hundreds of times more data.”
Even better? “When I pulled it all together,” said Olson, “our clouds lined up with a less-than-centimeter accuracy between Spicer’s and our upper and lower data. You would never find that kind of accuracy any other way. You could achieve it, but the cost would be exponential.”
Seamless Workflow Maximizes Efficiency
From there, Horrocks was able to deliver the MicroStation and TopoDOT files to the Idaho DoT. (The software exports to all common industry standard formats.) “To crunch all that data, it was about a week and a half for a team of four people to extract the full survey,” said Orson. “It’s a lot faster than it was a few years ago, I can tell you that much.”
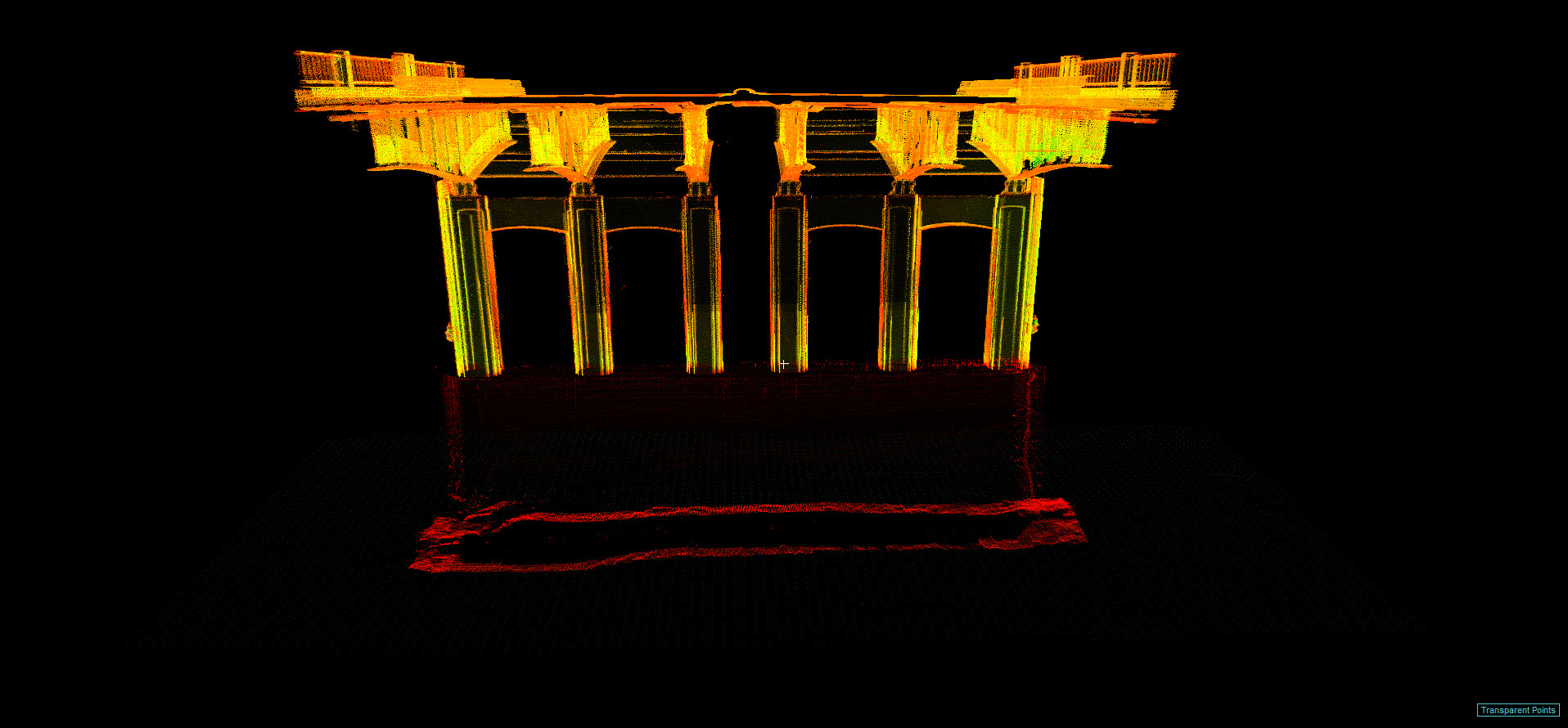
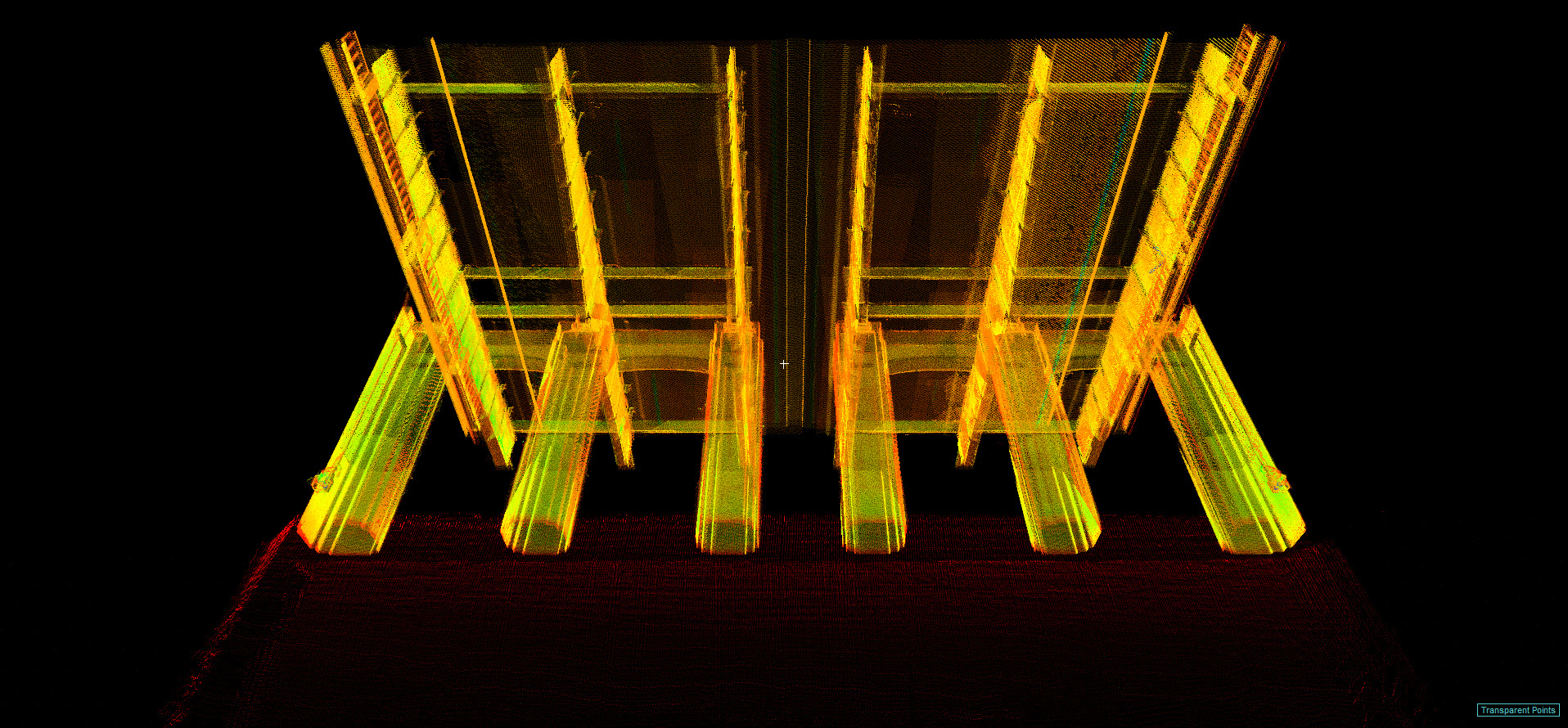
Leica Geosystems’ Jason Ellis provided some technical support on the job, as he’s been doing for survey teams for decades. Even he was impressed by the speed of collection in this case. “If I think back to learning field surveying with a transit and steel tape,” he said, “just the amount of time you’d use on small sites picking everything up—to go from that to collecting a mile of roadway data and the underside of a bridge in less than three hours total field time is just staggering. I’ll never get over the amount of data you can collect in such a short amount of time, and how accurate it is. It’s amazing.”
To learn more about how to maximize opportunities in your surveying business, please contact us.
———————————————————-
NOTE: The new Leica Pegasus TRK, launched in May 2022, brings even more opportunities for mobile mapping through its autonomy, intelligence and simplicity. Learn more about the Pegasus TRK here >
———————————————————-