A high-sensitivity slope monitoring system provides early warning of additional rock instability and failure during road repair work following a rockslide.
Fortunately no one was injured when 100,000 cubic meters of rock slid down a rocky scarp near a hydroelectric facility northeast of Campbell River, British Columbia, Canada. But it was certainly a dramatic and destructive event; the rockslide covered approximately 350 meters of access road and crushed and ruptured the penstock (the structure that conveys water to the hydroelectric facility powerhouse) in several places.
What pushed the rockslide over the edge is something of a mystery. Sarah J. Kimball, an engineering geologist at Vancouver-based BGC Engineering Inc., wrote in a technical paper on the slide that “strength degradation of the exfoliation surface is considered the major causative factor for the rockslide release as no apparent climatic or seismic triggers were identified.” Put another way, the rockslide was likely due to inherent underlying instability and failure along joint surfaces in the rock, making further slides possible.
To be effective, the monitoring system would have to identify small, dangerous movements on the slope and quickly—preferably instantly—sound alerts so that workers could evacuate, while avoiding too many false alarms that would impede the work.
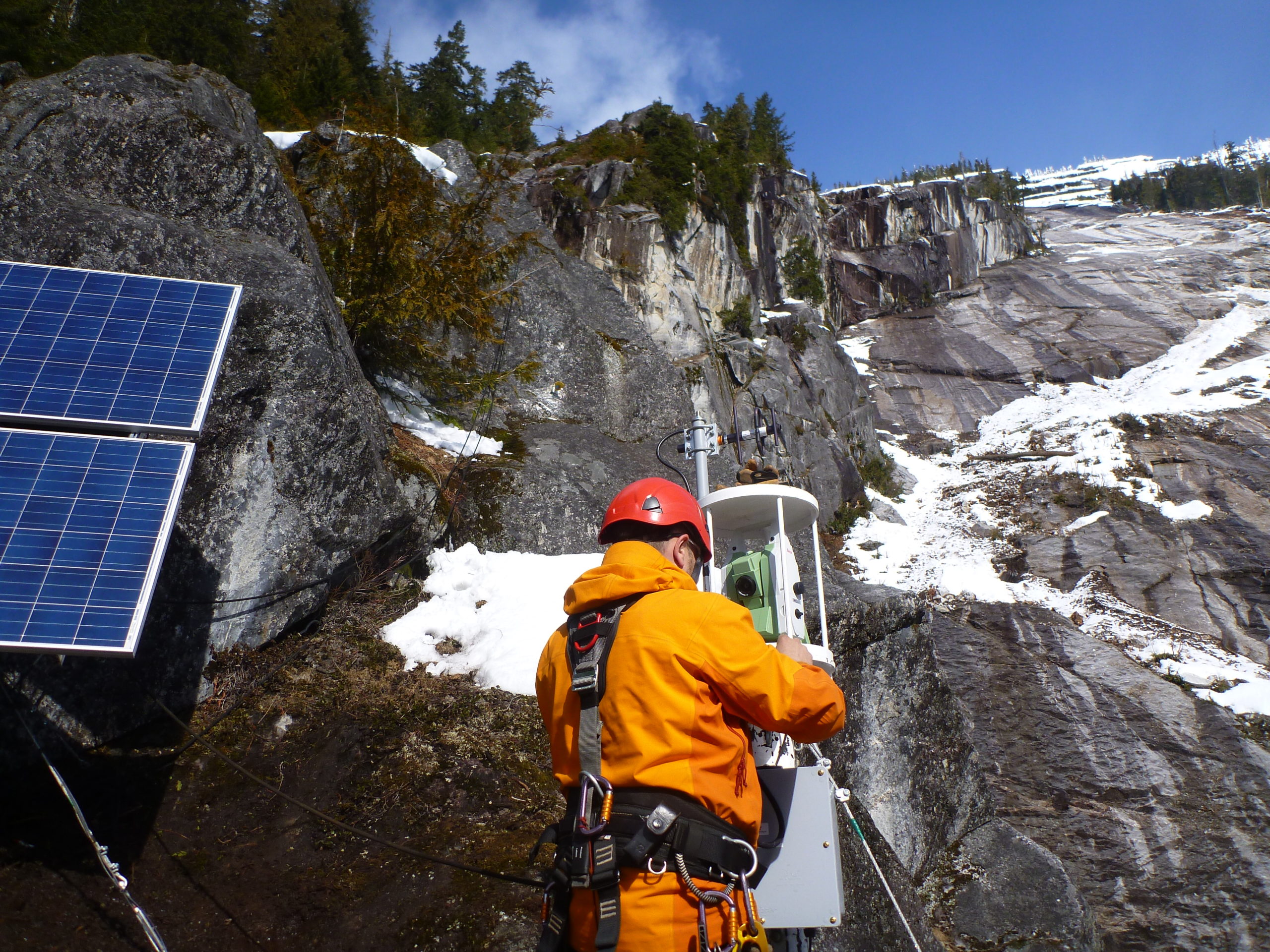
After the slide, the road and penstock needed to be uncovered and repaired, including digging up and replacing most of the penstock—a rather daunting undertaking when working on a steeply sloped mountainside that has definite potential to dump tons of rock unexpectedly. To protect workers and new facilities, BGC was contracted to design and implement a slope monitoring system to provide early warning of potential landslides during repair work. The firm came up with a combination of two monitoring systems that collected and analyzed near-real-time data. The systems were ground-based interferometric synthetic aperture radar (InSAR) and two automated electronic distance meter (EDM) total stations made by Leica Geosystems.
Installing the system presented a substantial design challenge. The rock slope between the road and the rockslide head scarp is quite large, covering about 1,350 meters slope distance and several hundred meters in width. Access was difficult, the site was in remote territory, and any installations would themselves be on steep and potentially unstable surfaces. And to be effective, the monitoring system would have to identify small, dangerous movements on the slope and quickly—preferably instantly—sound alerts so that workers could evacuate, while avoiding too many false alarms that would impede the work.
Installing Sensors—The Hard Part?
Onsite work began with the installation of an IBIS-M ground-based InSAR system in February 2013 about a mile from the rockslide slope. This location provided the best available vantage point of the slope area and of a large protruding rock on the slope dubbed ‘Wynona.’ The system was configured to complete a slope scan every six minutes and has a resolution of less than 1 millimeter. Weather algorithms were used to compute corrections for changing atmospheric conditions. Since InSAR data is quite sensitive, it was important to consider changes in environmental factors such as tree cover, snow accumulation, fog and cloudiness, and rainfall when interpreting the data.
In March 2013, the two total stations were set to monitor the slope and the lower face of Wynona. These were Leica TM30s, recommended by monitoring specialists Monir Precision Monitoring as the best available precision at long distances. One station monitored the head scarp from distances of 120-200 meters, and the second station monitored Wynona from distances of 250-350 meters. Ideally, prisms would have been set for even better precision, but this was simply not possible on this project; access was limited and the terrain was steep. Instead, reflectorless monitoring points were chosen—18 points for the first TM30, and 12 for the second—that were light-colored and on flat, dry surfaces achieved accuracies of 2.5 millimeters.
Flowing surface water, fog and cloud, and other atmospheric conditions occasionally made readings difficult, but the total stations were able to confirm some of the InSAR readings that were questionable. Basically, the redundancy of two systems was helpful throughout the project.
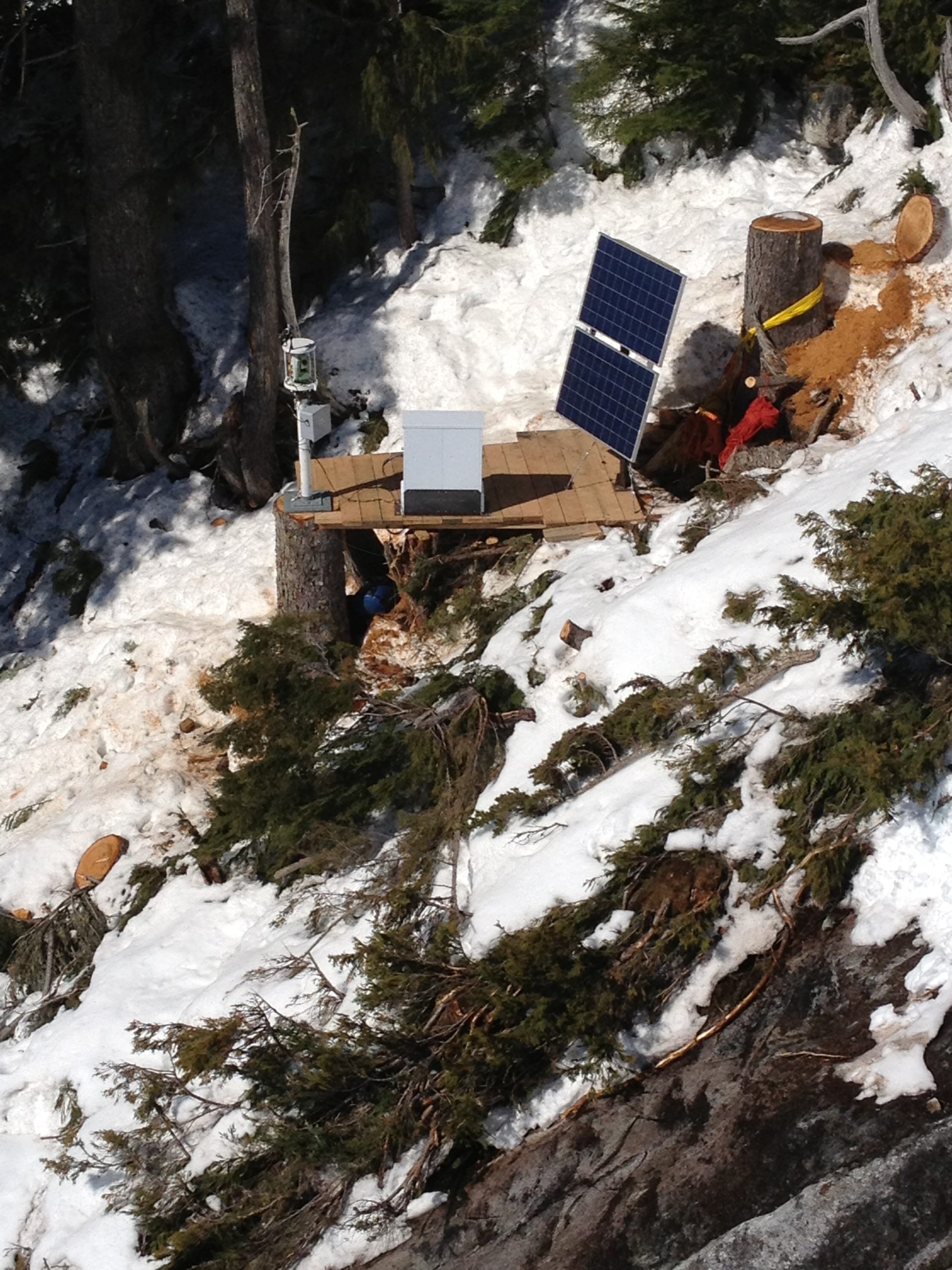
“Installation” is probably too mild a word for the work done by the installation crews. This is a remote site in rough terrain, very steep, with no access trails. Initial work was done with helicopters and rope support as log and 2×4 platform enclosures were built. Installation took weeks, though eventually the platforms allowed easier roped access to the sensor sites. Craig Hewes, PLS, director of technology for the Leica Geosystems Engineered Solutions group at the time, got personally involved. “Craig was great,” Kimball says. “He helped us set up the total stations for the best accuracy, and he was onsite for final commission—it was great customer service.”
There was one typical challenge of monitoring installations that wasn’t a factor here; security. “No worries about security, since there’s no way for the public to get to the site!” Kimball laughs. “And also, there were usually avalanche technicians and geotechnical staff around to keep an eye on the equipment.”
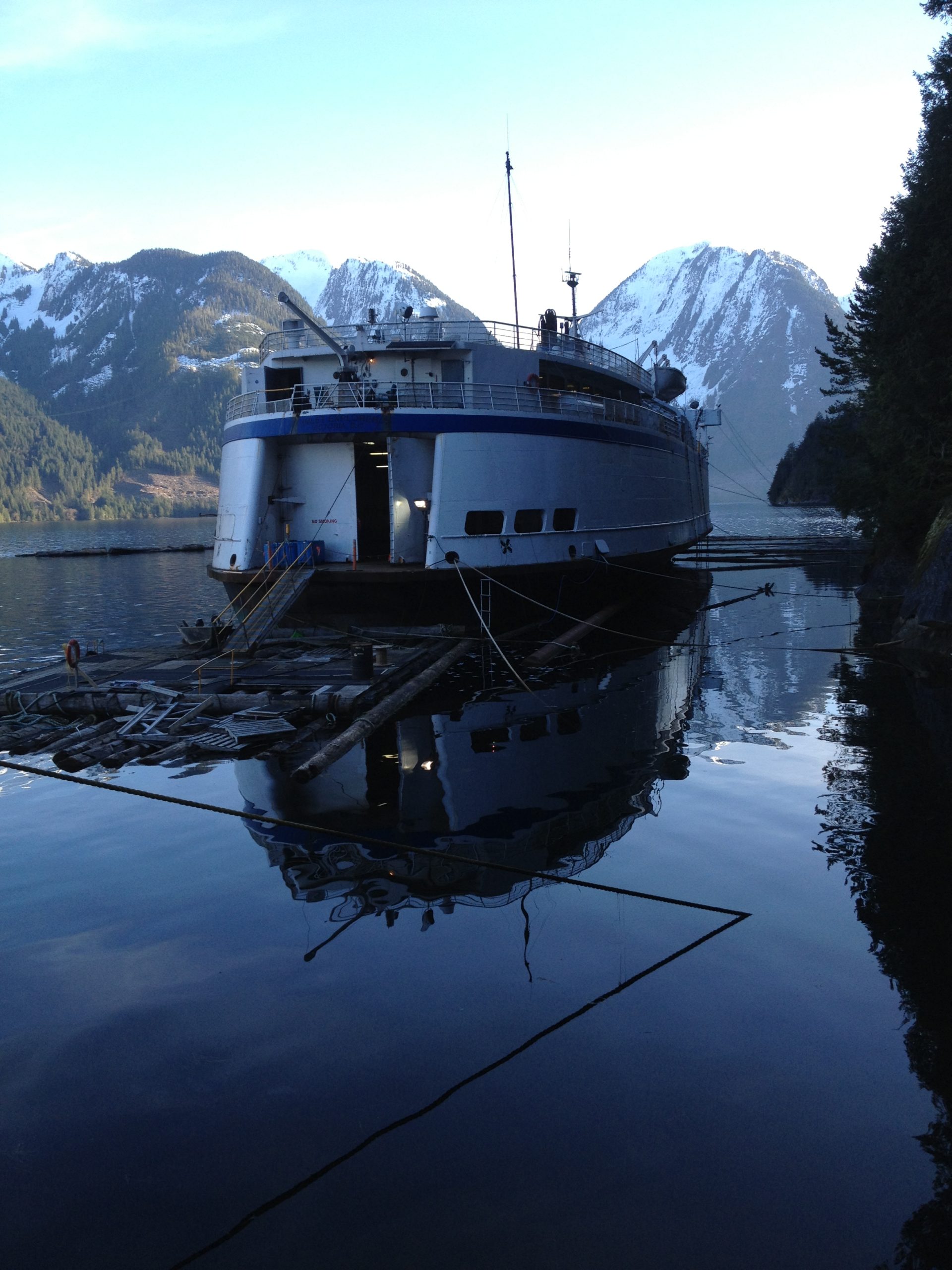
Monitoring and Alerting
Data generated by InSAR and the TM30s was transmitted to an office set up in a “Sea Can” shipping container near the work site. No attempt was made to combine the separate streams of data; rather, all streams were analyzed separately, with their own alert protocols, and acted as checks on each other. Given the stakes, the redundancy was appreciated by all concerned.
InSAR data was refreshed and transmitted every six minutes, and total station data was automatically refreshed and transmitted every fifteen minutes by the Leica GeoMoS software. The data was physically monitored during work hours by BGC staff, who were able to sound alarms—horns and sirens—if needed.
According to Kimball, alarm thresholds were established “on the premise that:
- the rockmass would deform internally if slope failure was imminent;
- the downslope rockmass velocities would accelerate prior to failure; and
- the acceleration would be measurable.
Line of site displacement vectors for the main slope and the Wynona block were calculated to correct for the actual component of movement observed by the total stations and InSAR. Five alarm levels were established for actual displacement vectors over 1 hour and 24-hour periods. The alarms would be sounded if velocity thresholds were exceeded over a defined slope area and time period (by comparing sequential scans).”
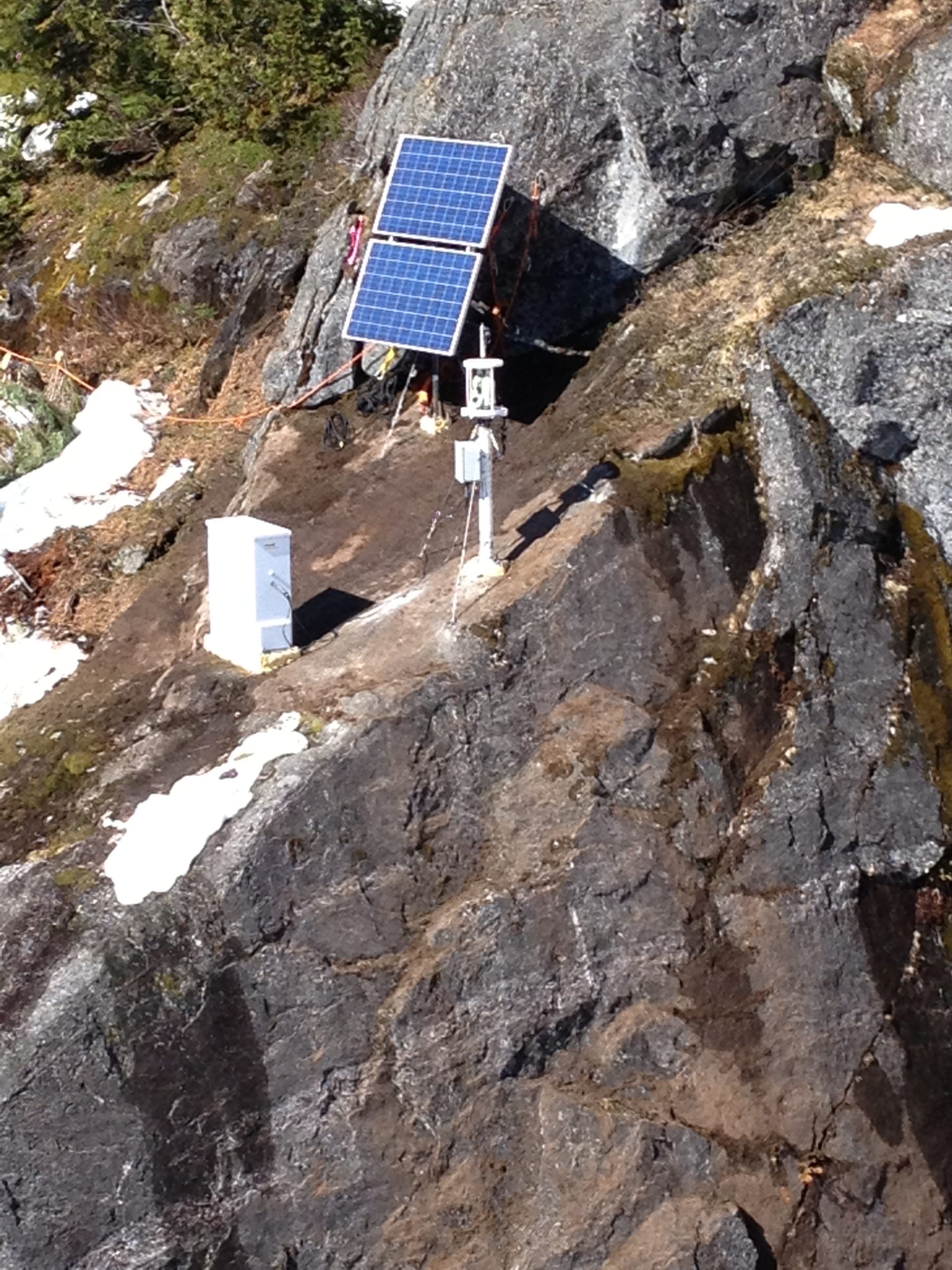
A Successful—and Safe—Repair
Using this methodology, no actual slope deformations indicating imminent failure were, in fact, observed. However evacuation alarms were sounded on five separate occasions, precipitated by InSAR alerts. After analysis, these alerts were attributed to atmospheric conditions resulting in false displacement in the data, rather than slope movement.
This would be a more exciting story if a new rockslide had occurred during the project and workers were saved by a last minute siren triggered by sensors. But the lack of drama indicates a successful monitoring project. By carefully and continuously measuring relevant spatial data during the road and penstock repair project, BGC Engineering was able to assure the safety of all the many contractors and subcontractors onsite, and they were able to do their work in a much safer atmosphere. And when thousands of tons of rock are literally hanging over your head, that counts for a lot.
To talk to one of our experts and learn more about solutions for surveying and monitoring, please contact us.